We are happy to bring you a guest post today from a lifelong and licensed boiler maintenance and inspection technician. Mark Decker possesses a wealth of knowledge about steam boilers and exhibits that knowledge for his customers at Sellers Manufacturing. With the spike in boiler incidents at distilleries we thought it would be a great idea to look at steam boilers and how they work. We asked Mark to give us the top 10 points of selecting and maintaining a distillery steam boiler. Should you have any questions, send Mark an email at mdecker@sellersmfg.com.
There are many types and sizes of boilers and the focus of this article is to cover fire-tube designs that are normally utilized in clean steam markets such as distilleries. Sellers H series clean steam boilers range from 293 to 8,800 lbs/hr of steam. Our standard design boilers can provide up to 31,050 lbs/hr of steam with pressures up to 300 psi.
Steam is a critical part of the distillery process and frequently overlooked when it comes to the design and safety of the equipment required. This article is designed to better educate the distillery owner on the use, maintenance and safety of your equipment and is meant to be an overview. Since there are many types of boilers on the market, you must consult with your boiler manufacturer for the safety of your particular equipment. This article covers only the boiler itself and not the ancillary support products required for the boiler room.
Select the correct boiler for your process:
- A typical steam boiler will require:
- Feed water and condensate return system.
- Chemicals to keep the boiler from scaling and eliminate oxygen pitting.
- A re-boiler (heat exchanger) to convert the chemical laden steam to clean steam to be utilized in your column.
- A clean steam boiler (Sellers H series):
- City water feed only. No feed water system or condensate return systems are required.
- No Chemicals are needed.
- A re-boiler (heat exchanger) is not required since no chemicals are utilized in the boiler and the steam can be utilized directly into your process (column or mash tanks).
- Start up and run periods costs:
- A typical multiple-pass steel boiler will typically have long start-up periods requiring the boiler to remain online when it is not needed for production. This is to help relieve any thermal stresses associated with the expansion and contraction of the boiler.
- Sellers Clean Steam boiler will create steam in less than 20 mins (from 50°f water) and can be turned off between batches or any time steam is not required. Thermal Stresses are eliminated by the design of the pressure vessel.
Sellers Clean Steam H series boiler w/cut away
Water Treatment and Maintenance:
Water treatment is critical for long life and safety of your boiler system. If your system is not a clean steam boiler, you must contact a water treatment specialist to insure that the proper chemicals are being utilized based on local water conditions. If you own a Sellers clean steam boiler, no chemicals are required and only a softener may be needed.
The following should be included in any water treatment plan:
- Prevent scale buildup or deposits that can reduce heat transfer and cause overheating of metal surfaces.
- Eliminate corrosive gases in the supply water.
- Prevent intercrystalline cracking or caustic embrittlement of the boiler metal.
- Prevent carryover and foaming of the boiler water into the steam piping.
- In addition to chemicals, pre-treatment (such as water filtering, softening and de-aerating) can be used depending on the feed water makeup at your facility.

Blow em down or blow em up!
Blowdown maintenance is critical to the safety of your boiler. Surface and bottom blow downs are typically used with steam boilers to remove any solids left behind. These solids will need to be removed by performing blowdown maintenance on your boiler.
- Surface blowdowns are utilized to measure the total dissolved solids in your boiler water and remove them from the surface of the boiler water. This is controlled by an automatic system.
- Manual blowdown valves are located at the bottom of the boiler and the low water columns to remove deposits that will accumulate much like a water heater in your home. This is a manual system that is often done once a shift. While the boiler is operating at low loads (but up to steam pressure), open the fast opening valve first followed by the slow opening valve. The frequency and time should be recommended by your chemical treatment specialist. If done too quickly, the boiler will not be properly cleaned. If opened too long, you will be wasting energy and boiler water.
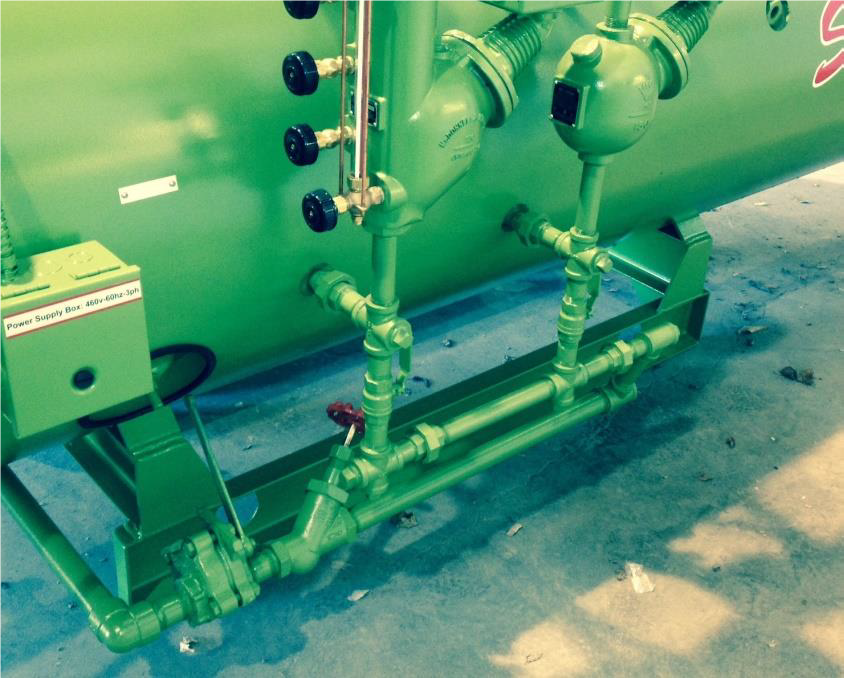
Low Water Cutout and Feed water controllers:
All boilers have one thing in common and that is the requirement of water being in the unit when it is fired. Although low water conditions are rare, you must perform the required maintenance to make sure the boiler low water cutout switches and pump controls are working properly. Boilers will have a minimum (two) devices to provide back-up in case of a low water condition. There will also be a gauge glass showing the water level in the boiler. If water is not in the gauge glass, the boiler should be OFF! It has been said that all boiler low water failures can be linked to improper maintenance or tampering.
- Primary low water controls are typically a float (can be a probe) within a bowl that measures the level of water in the boiler and will send a signal to the feed water system to bring more water into the boiler. In addition to the feed water control, it will also utilize safety switches that will shut the burner off in the event of a low water condition.
- Secondary low water controls will provide back-up to the primary and will incorporate safety switches to shut the boiler off should the primary control fail.
- The external piping that the low water controls are located are called a water column. It is critical that these water columns are also blown down to remove sludge buildup in the bowls that may limit the float from operating properly. Open the valves slowly as to not damage the floats inside the bowls. Again, the time duration and frequency should be recommended by your chemical specialist.
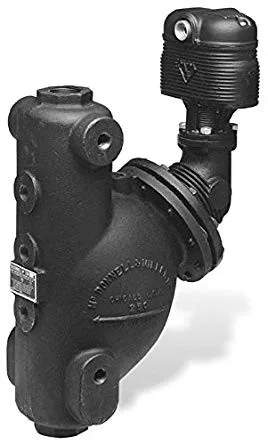
Gas regulators and valves:
Components of the pilot and main gas train consist of the following:
- Pilot and Main gas regulators are used to control the gas pressures to the smaller pilot and main gas valves.
- Pilot gas valve (typically a solenoid) to turn the pilot flame on and off.
- Main gas valve(s) are usually motorized gas valves that will also incorporate a safety “proof of closure” switch. Should the valve not close 100%, the P.O.C. switch will tell the combustion control to lock out.
Gas Pressure Switches:
Depending on the local codes and size of your boiler, your unit may have a set of Low and High gas pressure switches. These switches are designed to shut the burner off if the gas pressure increases or decreases beyond the switch settings. Without the pressure switches, a dangerous condition could exist as incoming gas pressures could fluctuate causing the combustion settings to change creating high CO (carbon monoxide) levels or sooting of the boiler.
- Low Gas Pressure switch measures the lowest gas pressure. It is set to 10% lower than the actual gas pressure.
- High Gas Pressure switch measures the highest gas pressure. It is set to 10% higher than the actual gas pressure.
Combustion Air Fan Proving switch:
The combustion air proving switch measures the amount of pressure created by the combustion air fan. If the powered fan should experience a failure, the combustion air switch will lock the burner out so that the pilot or main gas valves do not open.
- Set when burner is running its lowest firing mode by a qualified technician experienced with the model of air switch on your boiler.
Pressure Controllers:
A modulating boiler will have 3 steam control devices. Operating, Modulating and High Limit. Today’s linkageless control systems typically utilize the Operating and Modulating controls in one unit. The boiler inspector may want to inspect internally the piping that these controls are mounted on.
- Operating Pressure Control shuts the boiler off when the pressure reaches the set point and then turns the boiler back on when it reaches the differential (lower) pressure. This occurs automatically while in the run cycle. As an example, you may want the boiler to shut off at 12 psi and then come back on when the pressure drops to 8 psi.
- Modulation controllers will control the firing rate of your boiler. If the boiler is to shut off at 12 psi, you may want to set the modulation controller to be at low fire position at 11 psi. As the pressure drops the firing rate will increase keeping the boiler online and holding the pressure to the desired 11 psi.
- High Limit Control is set higher than the operating control. If the boiler should fail to shut off at 12 psi, the high limit control will shut the boiler down. It is a manual reset device.
Combustion Control:
Today’s solid state control systems are designed to provide safety and efficiency. There are too many on the market to be able to give advantages of each, but most operate in the same manner.
- Linkageless control systems allow you to set the combustion air/fuel curve precisely where it will achieve maximum combustion efficiency. Typical fuel savings are 3-5% over a linkage style burner.
- Safety interlocks. The control system will check the limits and operating circuits to make sure your boiler is ready to be safely fired. Should a safety device fail, today’s controls will let you know when and what device it is.
- Flame monitoring is another important function that the combustion control performs. If a pilot or main flame fails to ignite, the combustion control will lockout the burner. It also monitors the unit when in the standby mode to make sure a flame does not exist when there should not be one.
- Self-diagnostics can be very helpful when trying to troubleshoot the combustion control itself. The control system will tell you if a component in the control has failed and needs replaced.
- Communication capabilities allow you to monitor your boiler from a remote location. Mod Buss, Lonworks, Bacnet and Metasys are a few of the communication logics the control systems are capable of communicating with.
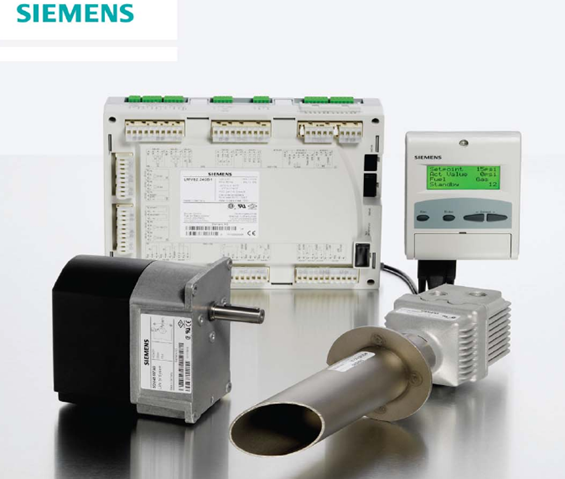
Boiler room requirements:
- Keep the boiler room clean. Repair any fuel, water or steam leaks quickly. You should be able to move about in the boiler room easily. A boiler room is not to be used for storage.
- Never close fresh air dampers to the boiler room. As a general rule, you will need 250 square inches per 1,000,000 BTU/hr of input. (consult with local codes). It’s very common to find the fresh air dampers closed or blocked during the winter months. If other equipment is affected by the cold air, you can divert the air with ducting but you must not reduce the total area of the required fresh air. Insufficient combustion air will affect combustion and could lead to explosions, injury or death!
- Internal boiler inspections are usually required once per year on a steam boiler. The fireside and waterside of the boiler must be opened and all water column plugs removed for the boiler inspector. Fireside should be inspected for refractory cracks or failures and boiler tubes for signs of leakage. Waterside should be flushed out and your chemical treatment specialist may want to look inside as well.
- Boiler service technicians are critical for maintaining your equipment. Many of the adjustments and maintenance items should be performed by an individual trained and experienced with your control systems and equipment. Combustion adjustments must be made by an experienced technician with the proper equipment.
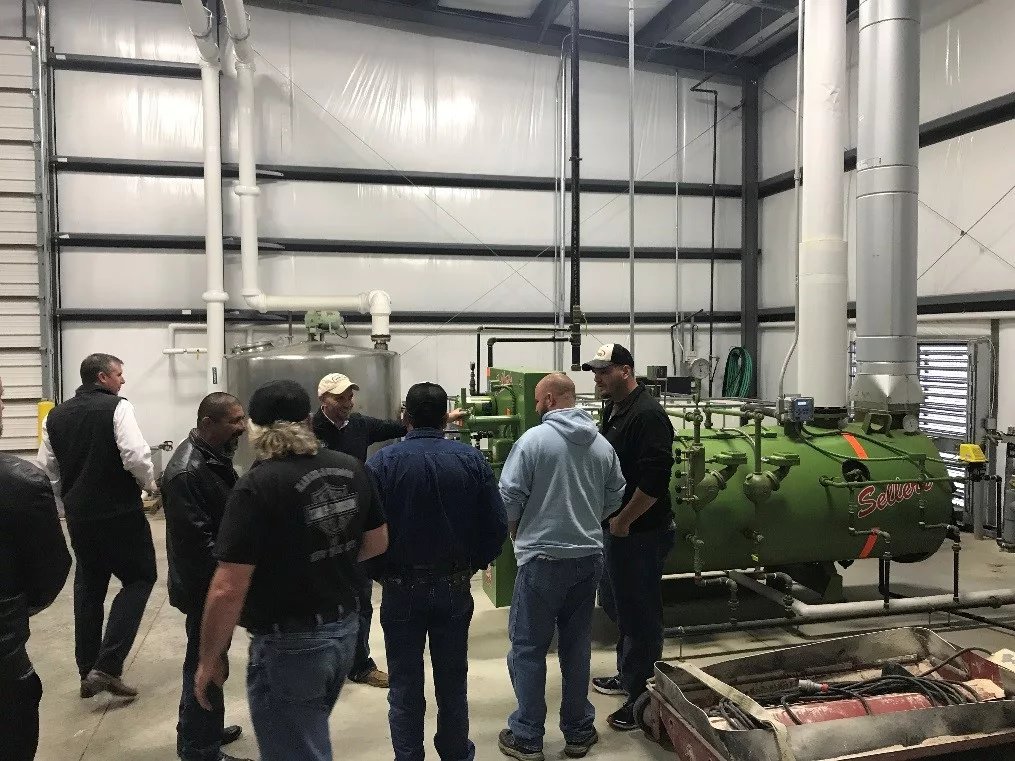
Those are the top 10 points of selecting and maintaining your distillery steam boiler. There are many types and sizes of boilers and the focus of this article was to cover fire-tube designs that are normally utilized in clean steam markets such as distilleries. Sellers H series clean steam boilers range from 293 to 8,800 lbs/hr of steam. Our standard design boilers can provide up to 31,050 lbs/hr of steam with pressures up to 300 psi.