We’ve been wrapping up all our rough-ins, getting inspection sign offs for plumbing, mechanical, electrical, fireplace, and fire sprinkler. We also just got the exterior painted which has been exciting!
Rough Inspections
All in all, the rough inspections went pretty well:
Mechanical– Corrections included add some taping to bathroom exhaust ducts (local code amendment), and updating our Manual D to reflect the as built mechanical. A Manual D is a standard system of designing an HVAC system for a house. This was required for plan review, but it is normal to make many adjustments in the field. So, the inspector required that the manual D be updated to reflect field as-built. Our HVAC contractor took care of this.
There was some careful coordination needed for dealing with roof penetrations and the metal roof. We had a few bathroom and kitchen exhaust roof penetrations go in before that part of the roof. But, when we were ready to put in the metal roof, it did not align with the ribs. We want the penetrations to happen right in between ribs, not on the ribs. So, HVAC had to shift their penetrations in. Moral of the story is- if you have a standing seam metal roof, have the roof in first, then do penetrations!
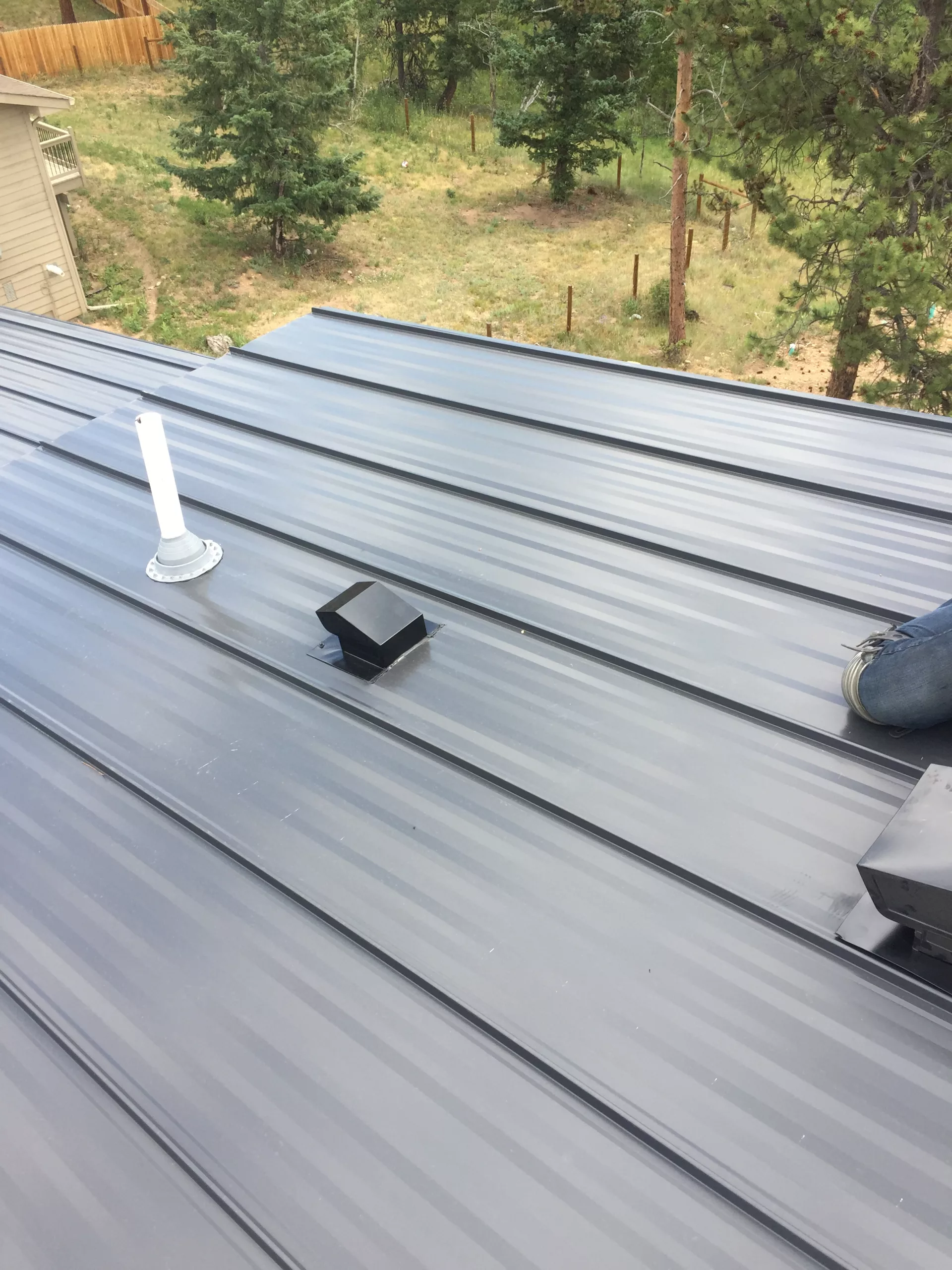
Plumbing- This went pretty smooth as well. Inspector had a few corrections like isolating water lines from touching ducts. This is so that heat in duct will not warm up a cold water line. Also, we have some water pipes in the wall between an inside room and the garage. Since the garage is unheated, its considered as if it is outside. And water pipes are not supposed to be in outside walls because of freezing. But, the inspector is allowing it here as long as we add extra spray foam insulation surrounding the water pipes in this wall.
Electrical- This one passed without any comments! woohoo!
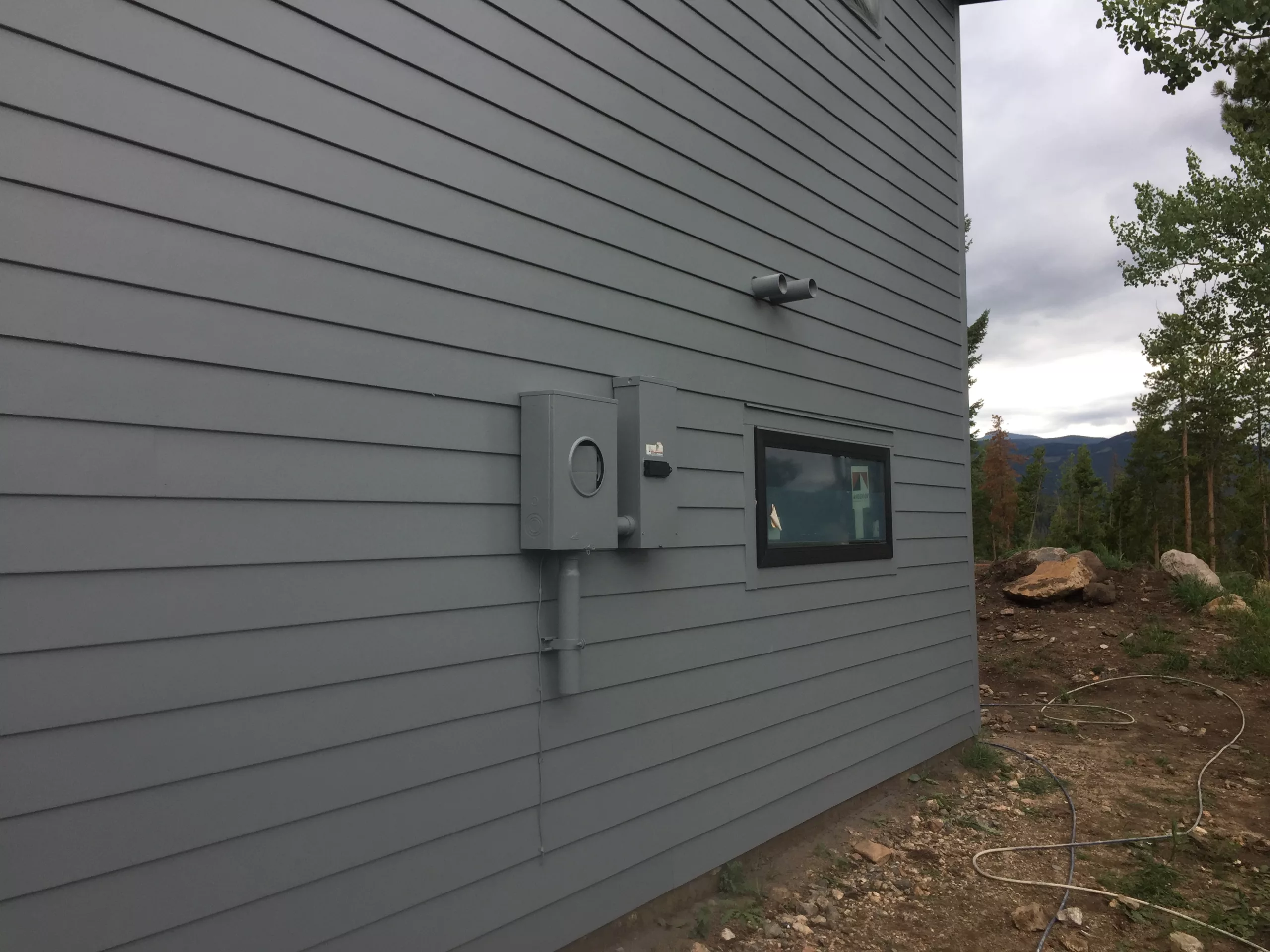
Fireplace- Our first inspection failed because we didn’t have firestopping completed. Basically, the void space that the fireplace sits within has to be completely encapsulated so that air or fire can not travel out of this space into another wall or ceiling cavity. We fixed this by simply adding some plywood fireblocking and some spray fire foam to fill in cracks/ gaps.
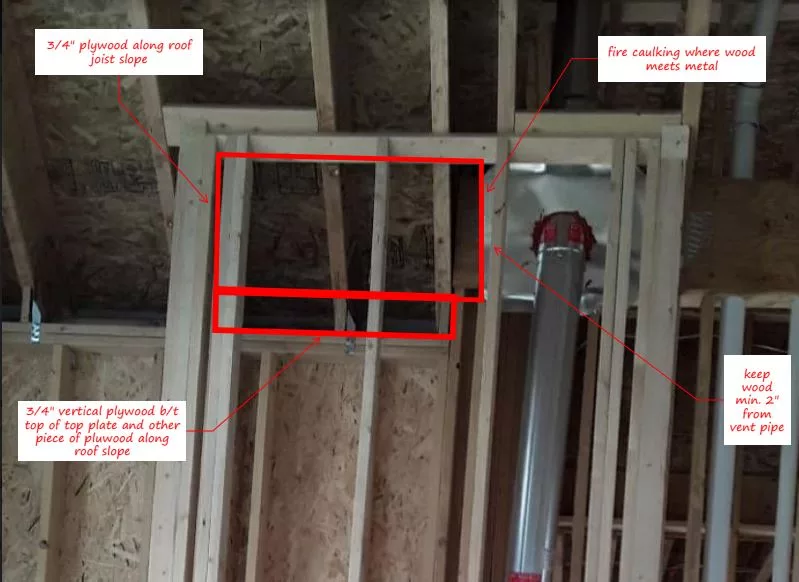
Fire sprinkler- This one also passed without any issues. We waiting until water was turned on so that they could charge the sprinkler lines and do their “hydro” test which essentially pressurizes the lines and makes sure the pressure does not drop over time.
Speaking of FIRE……….
About 2 weeks ago, a wildfire broke out on Elephant Butte mountain just a few miles from us. It spread very quickly, reaching 50 acres within a few hours. The evacuation zone was all the way to brook forest road, just about a half mile from us. It was a tense 24 hours.
Luckily, the skilled firefighters in our community battled the blaze aggressively and got it under control within a day or two. A bunch of rain helped as well. They even had a helicopter going back and forth from Evergreen Lake with water to douse the blaze.
Thank you firefighters for everything you do keeping us safe! There were no reported injuries and no structures burned.
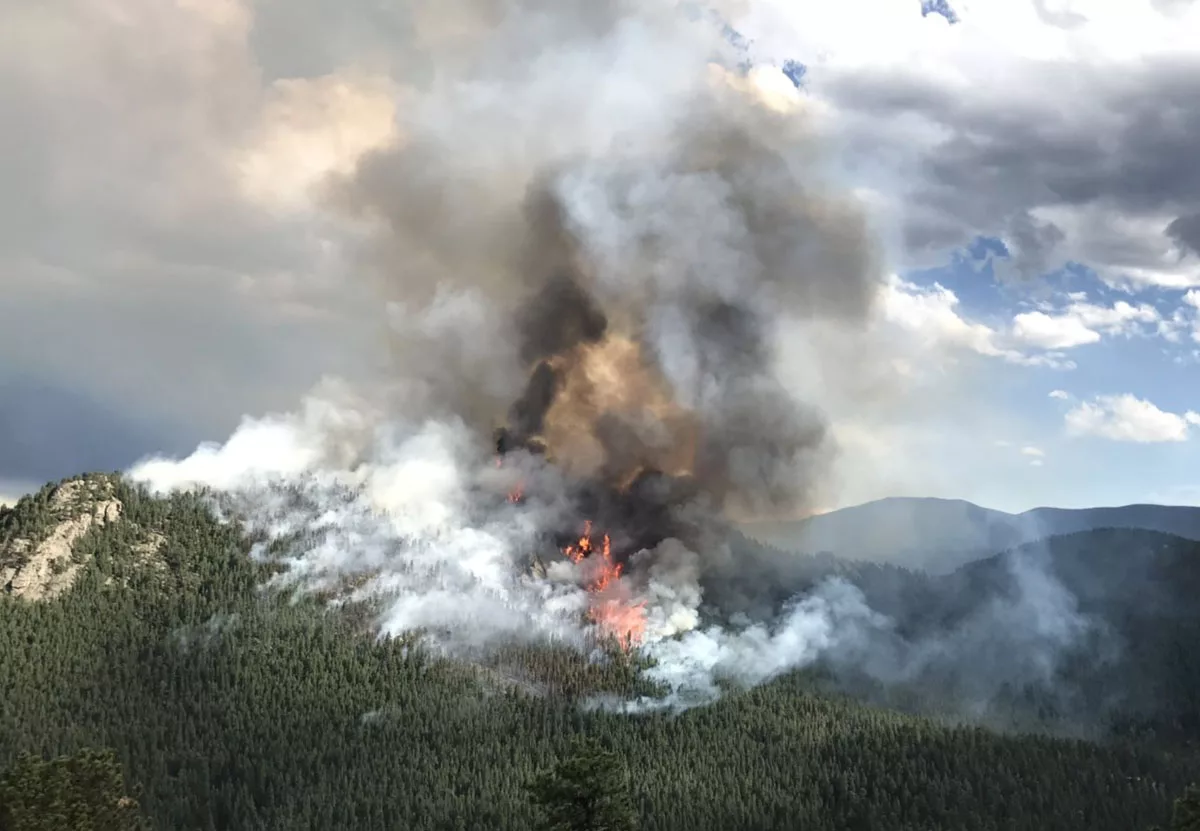
Water- Also, we got our water tapped, and turned on! There was a few issues with our water entry that we had our plumber put in. First, there were bleeders on the entry valves which the water company doesn’t allow, so our plumber had to replace those with non-bleeder valves. Then, the yoke that the meter gets set in was the wrong size. I had our water company switch that out. But, we finally have water now!
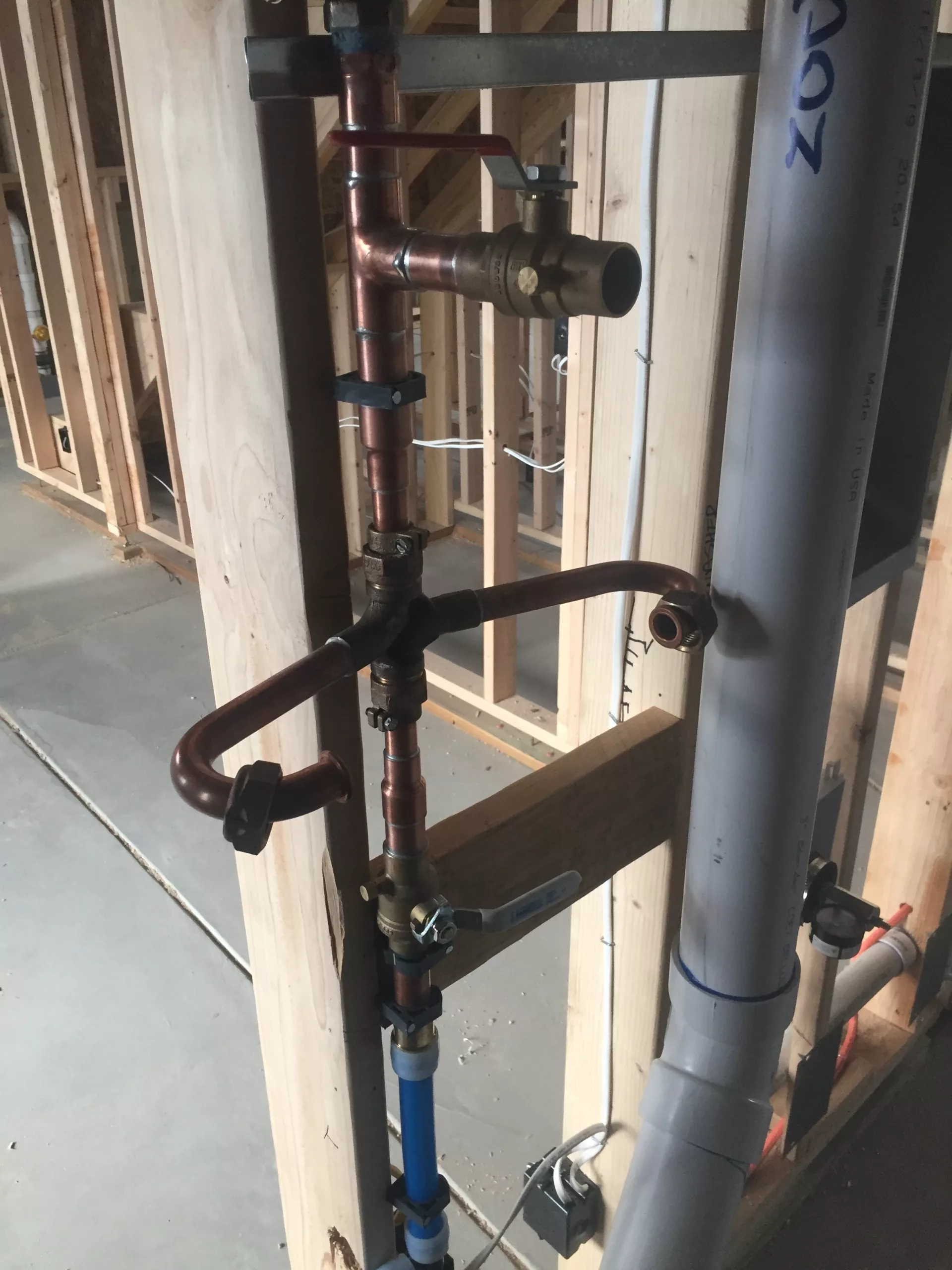
Painting
We got our exterior painted! This really makes the house look nice. They worked pretty quick and seamlessly.
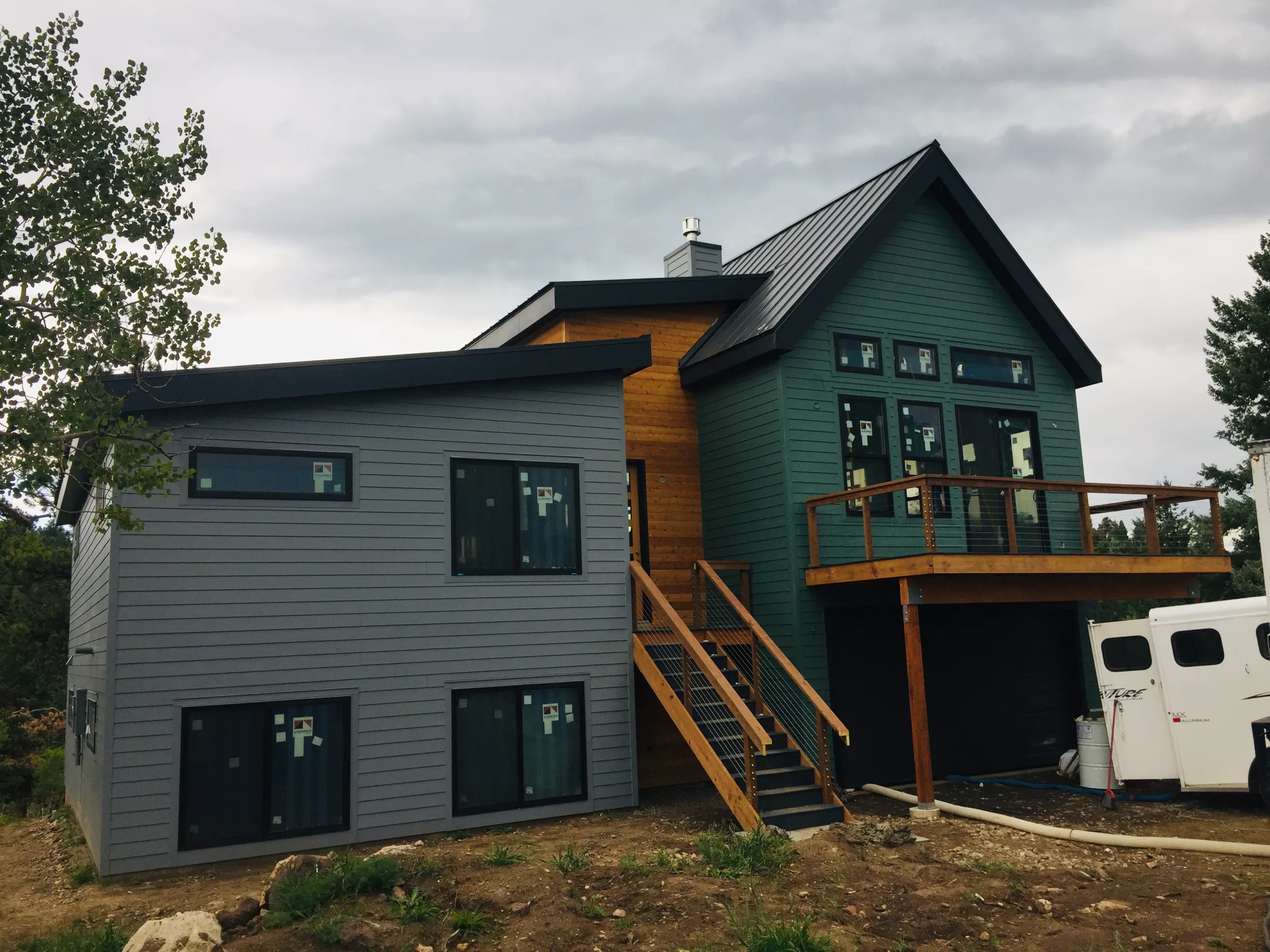
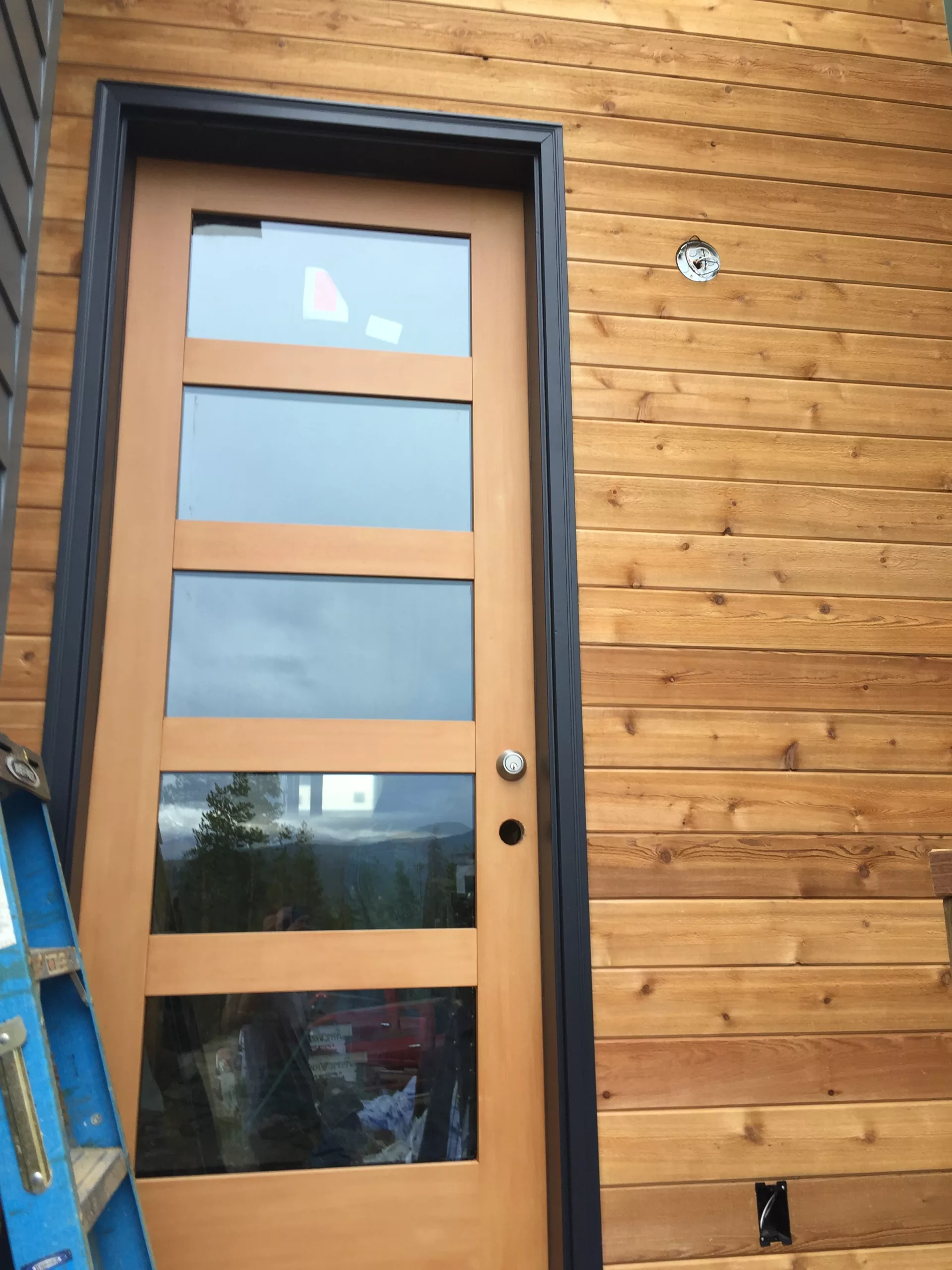
Insulation
Insulation went in this week. Now our house will be warm and cozy during our those snowy mountain winters!
We’ve got about 4″ spray foam close cell insulation on the roof with the remaining 10″ blown in fiberglass. This achieves about R-60 (R-49 is required) Then, the walls are mostly blow in fiberglass (R-23), with spray foam at rim boards.
Insulation went in pretty quick. It was a mess, but they should be cleaning it up!
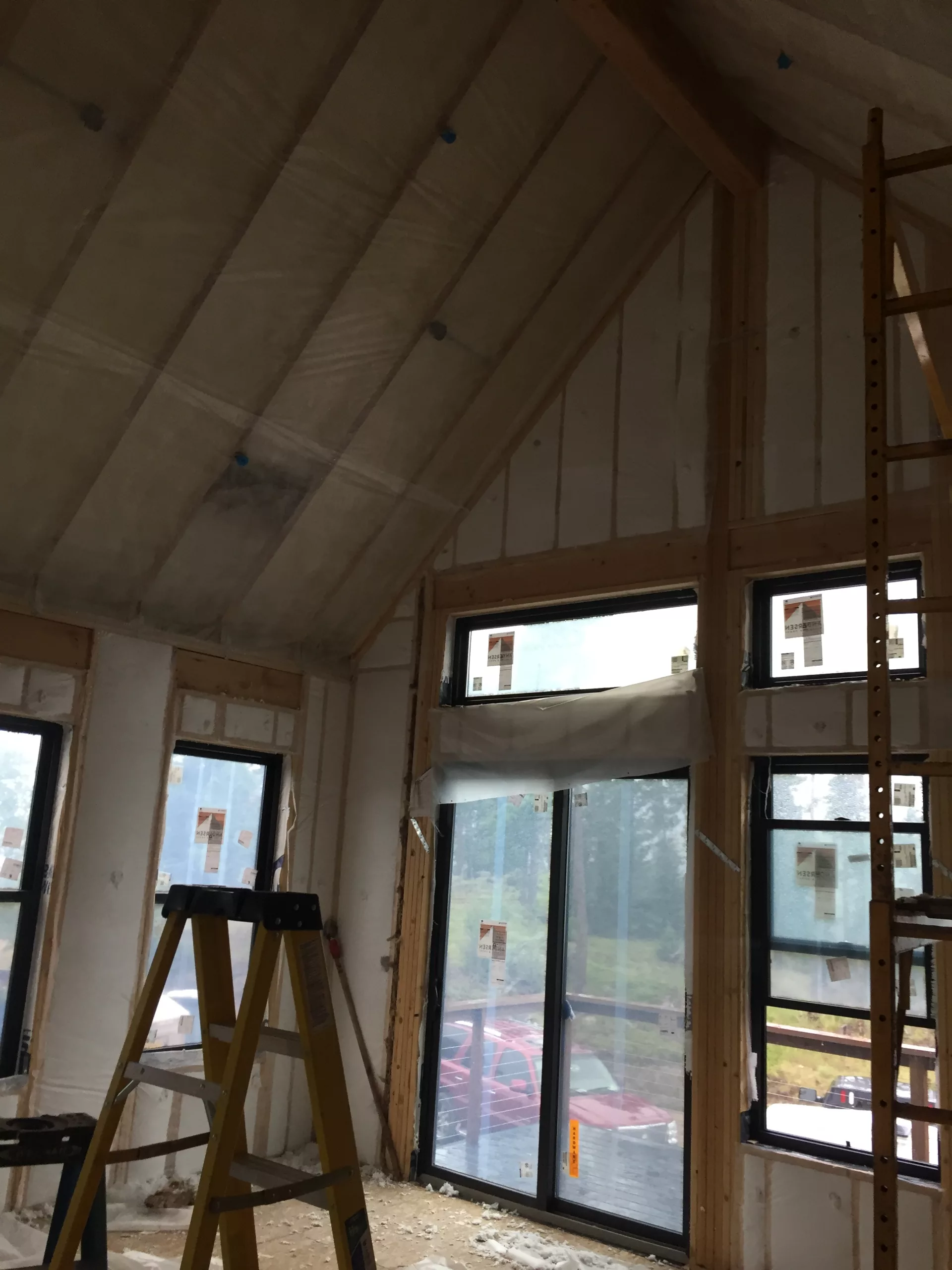
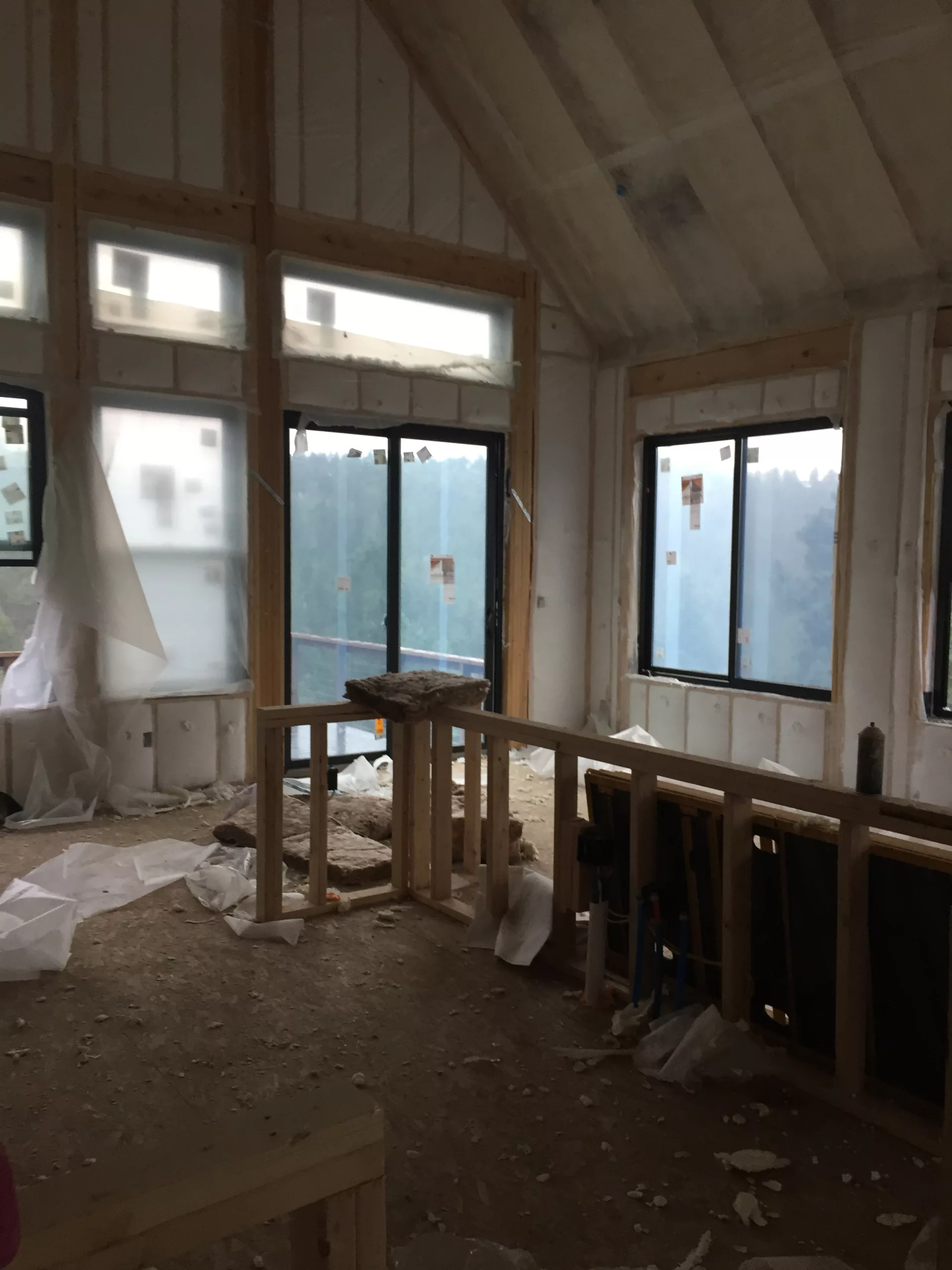
Steel cable railings
With the help of my husband and dad, we have been installing some cables to complete the deck guard rails. This cable system uses an easy to install system, but it is still time consuming!
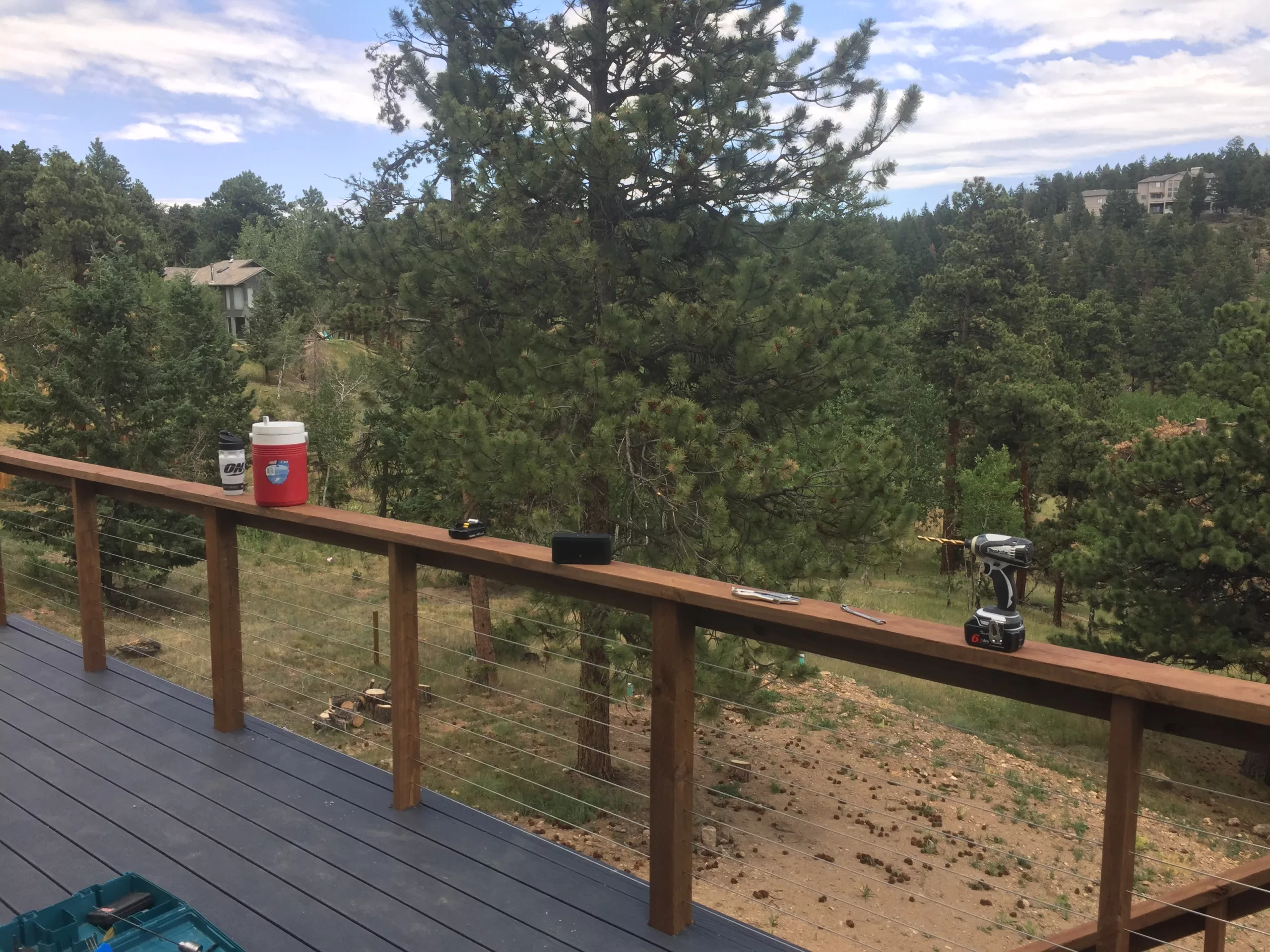
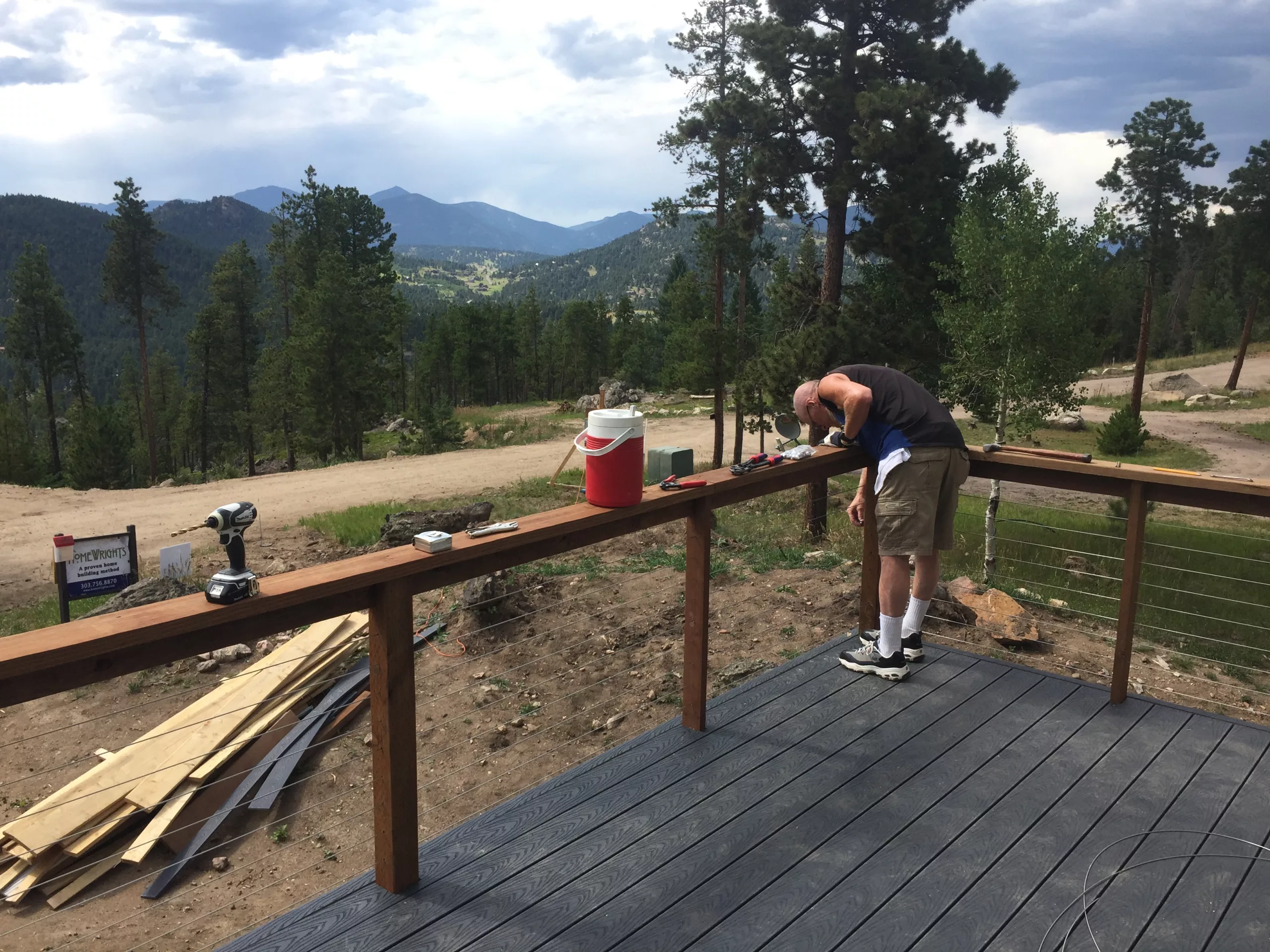
Next step (next week) is drywall! Can’t wait to actually have walls. Then it will really feel like a house.